WHERE IS IT USED?
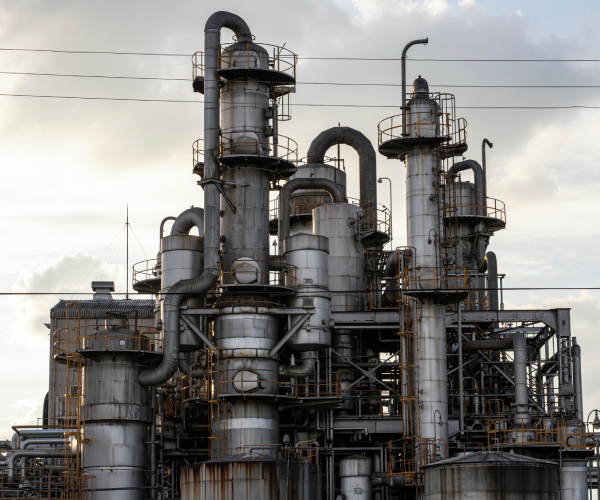
Industrial Piping and Fittings
Rubber gaskets are often used in industrial plants for utility and
chemical processing lines. These gaskets are limited to
low-to-medium pressures. Most rubber gaskets are limited to
around 150 psi (10 bars), while for some engineering-grade
types such as PTFE it varies.
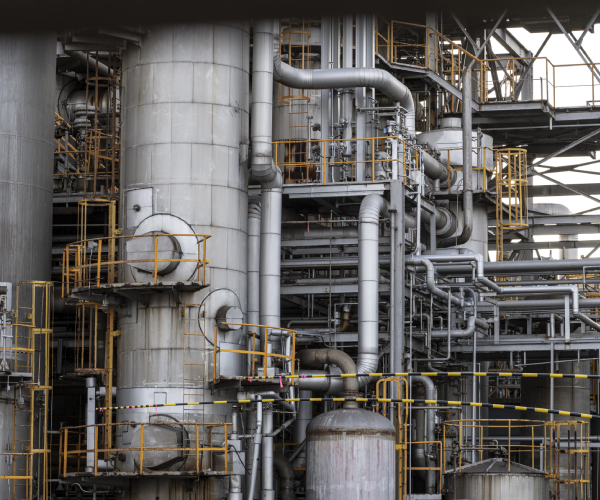
Power Plants
When selecting rubber gaskets for power plant applications, it is
essential to consider factors such as temperature resistance,
chemical compatibility, and the specific requirements of the
application. The choice of the right gasket material and design
is crucial to ensure long-term reliability and safety in power
plant operations.
FEATURES AND BENEFITS

Exceptional Elasticity
Conforms to irregular surfaces for a secure, airtight seal.

Insulation Properties
Effective sealing against sound and electrical conductivity.

Cost-effective
Economical and customizable, a preferred choice for manufacturers.

Elasticity, Durability, Chemical Resistance
Key features ensuring effective and lasting seals in diverse industrial applications.
MANUFACTURING PROCESS
Manway gaskets are manufactured through several key steps, starting with selecting materials and ending with final inspection. We will explore every step, illuminating the complexities of making manway gaskets.
The material used is determined by the specific application, elements such as temperature, pressure, and the type of fluid or gas to which the gasket is exposed. To create the appropriate shape and dimension for the manway gasket, the raw material must be cut or molded. Precision is required at this stage to ensure a proper fit and seal when the gasket is fitted. Die cutting and compression molding are the most popular methods of shaping manway gaskets. Die cutting involves stamping gasket patterns from prepared material with a die, whereas compression molding forms the gasket within a mold using heat and pressure. Each process has advantages and is chosen according to the material and manufacturing requirements
Manway gaskets are manufactured through careful material
selection, precision shape, quality testing, and ongoing
improvement. These techniques work together to produce
dependable, high-performance gaskets that are critical in
maintaining the integrity of industrial equipment.